The Renaissance Services “A Team” showed the colors at the Military Additive Manufacturing Summit & Technology Showcase in Tampa while local sports fans were celebrating the hometown Bucs’ playoff victory over the Philadelphia Eagles. The Summit & Showcase is the nation’s largest aerospace and defense 3D-printing event. This year, the 8th annual show was a magnet for military, government, aviation, and 3D-printing industry people alike.
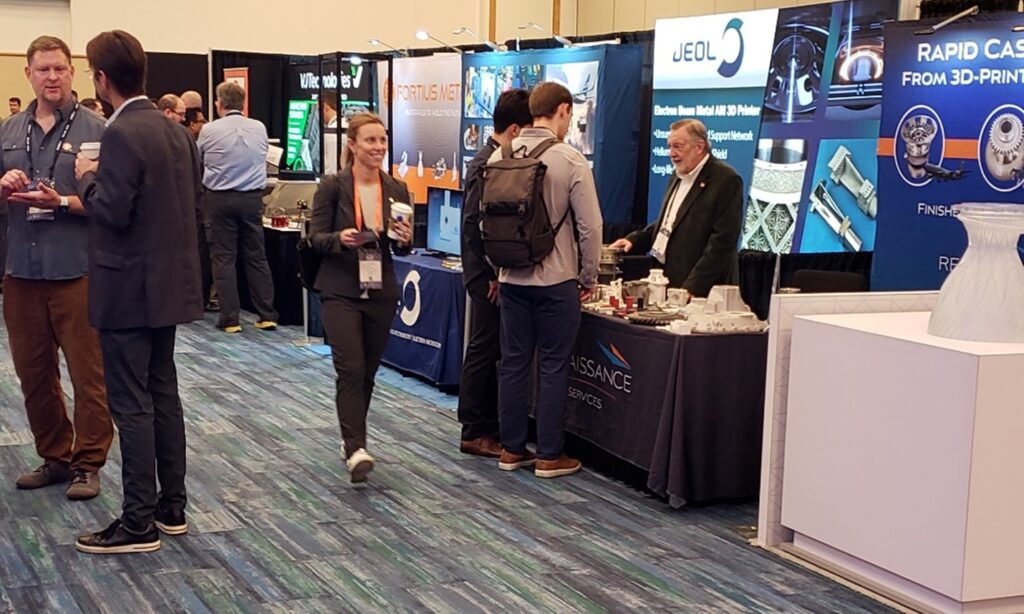
Don Deptowicz gets visitors and a friendly side-glance from an attendee at the Military Additive Manufacturing Summit & Technology Showcase. Credit: Rick Pressley
Renaissance Services’ booth at the Summit & Showcase displayed the company’s latest 3D-printed ceramic tooling and process aids. RSI benefited from a good location and from great exhibits.
And from great parts makers and exhibitors. Director of Programs Rick Pressley and Don Deptowicz, a veteran engineering and manufacturing consultant, represented Renaissance Services at the big-time military additive manufacturing convention. They were able to show off some of RSI’s most complex 3D-printed ceramic mold tooling and finished parts.
Pressley and Deptowicz talked with military, major aviation, and additive manufacturing contemporaries at the confab. In a clinical after-action report, the duo said they had many leads and multiple visits from multiple attendees.
Again, rapid parts delivery was the Renaissance Systems calling card that brought attendees to the RSI booth.
Several attendees talked with Pressley and Deptowicz about making test parts. Others were amazed, they said, about being able to obtain parts that have successfully undergone a rigorous service assessment in accordance with defense agency policy.
“(Military and civilian clients) are always receiving castings for machining. These (parts made with Renaissance Services ceramic additive manufactured mold tooling) “give them parts that have been validated for service usage,” Deptowicz said.
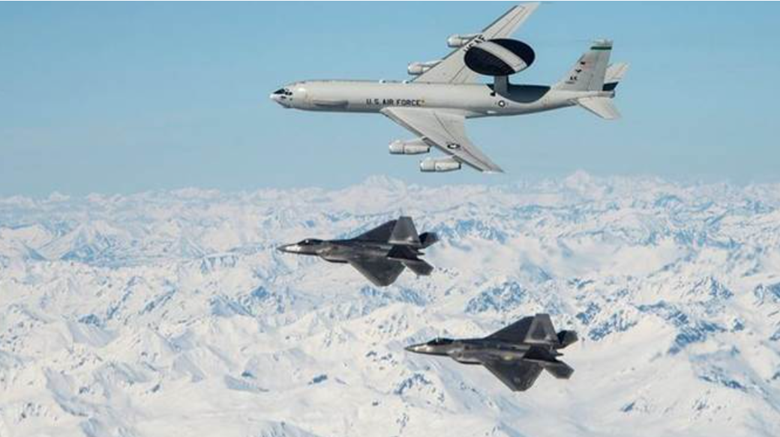
A Boeing E-3 Sentry land-based AWACS aircraft is flying over Alaska with two F-22 Raptor fighter escorts. Renaissance Services reverse-engineered and made gearbox covers for the AWACS aircraft. Credit: US Air Force
At least one major aviation manufacturer, they said, talked with them about rapid casting of newly-designed parts as well as legacy parts. Engineers from another heavy hitter in the aviation field, they said, picked their brains about 3D-printing of ceramic molds for newly designed parts.
Pressley and Deptowicz noted, “Although 3D metal printing is being pushed as a ‘silver bullet,’ industry is realizing that it is very hard to do.”
“A differentiator that was noticed by attendees,” they reported, “was our ability to get parts approved for use in service (TF33-P100) as well as testing of other parts in a full up functional assembly (F-15 Electrical Chassis, KC-135 AIG).”
“(Our parts) can get through a technical review in 15 minutes.”
Pressley and Deptowicz said there was a great deal of interest from Army, Navy, and Marine officials at the confab. (Air Force people also stopped by to visit and to get info. But the two expect that, as additive manufacturing has been a steady USAF interest.) They said they were happy to assure the military people Renaissance Services’ approach to parts making for the aviation industry would work for them, too, in their desires to have parts made for marine vessels, ground vehicles, and weapons systems.
Deptowicz and Pressley said the military attendees paid a lot of attention to what they had to say. They said the military attendees spent considerable time checking out the Renaissance Services exhibit and asking solid questions.
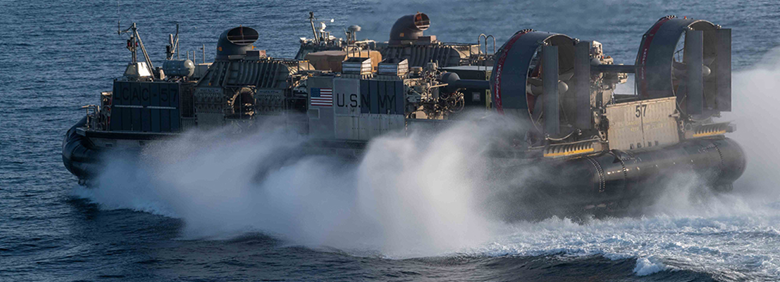
US Marine Corps landing craft. Credit: US Marine Corps
U.S. Marine Corp officials could have established a beachhead at the Renaissance Services booth, they were there that often and doing serious recon.
But they weren’t alone, Pressley and Deptowicz said. They noted Army officials queried them about making parts for the M1 Abrams main battle tank, which has been in service in various iterations since 1980.
The XM1202 Mounted Combat System was supposed to put the older Abrams tanks out to pasture, or to other armies’ inventories, or to scrapyards. But the US government cancelled the change. The US Army is still using the M1 Abrams tanks and has committed to upgrading them with improved optics, armor, and firepower.
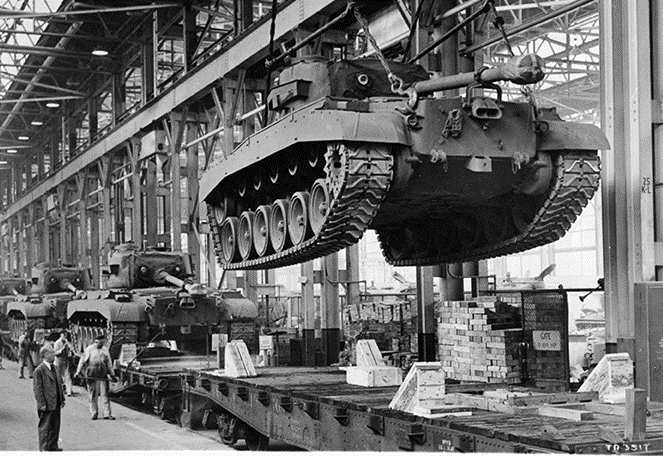
Pershing tanks being loaded onto flatcars, Chrysler Tank Plant, Detroit Arsenal, Warren Michigan. Credit: US Army and Chrysler. The workers built 6656 tanks in 1944. Of these, 3584 were the new Pershing models. Chrysler also sent a rebate check back to the government for $10,926,000 due to the decreased costs associated with higher production! Source: “Chrysler helps build the arsenal of democracy: M3, Sherman, and Pershing Tanks” by Chrysler buff and author Curtis Redgap, 2006
Soldiers and Marines use shoulder-fired Javelin antitank missiles. There were inquiries about making parts for these missiles.
Deptowicz added there were inquiries from Navy procurement officials about making legacy parts for ships. He said it irked him that multimillion dollar submarines had to be drydocked for lack of relatively inexpensive replacement parts. And, based on the professional interest of the Navy people, it is likely it irks them too.
He said there were also inquiries about corrosion control and surface treatments for metal parts.
The Renaissance “A Team,” without dropping names, were happy to field questions, meet quietly, and/or get leads from representatives of the Air Force, Army, Navy, DLA, and OSD. They were also happy to talk turkey with agents of quite a few manufacturers.
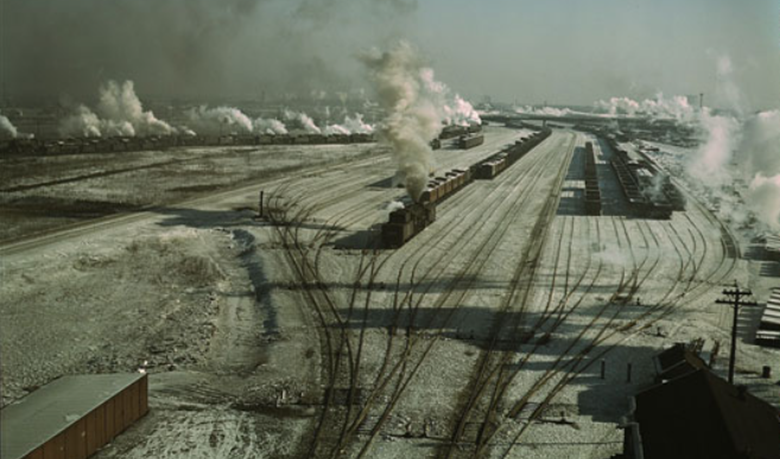
Chicago and North Western Railroad Proviso Freight Yard, 1944. These freight trains were loaded with war materiel as well as with food and goods for the American people. This facility was the largest railroad freight yard in the world. Credit: Jack Delano, US Farm Security Administration.
“It’s not a supply chain, it’s a supply train!” Deptowicz maintains. “Chains break. Trains move things!”
Renaissance Systems stands ready to assist the supply trains of commercial and military customers so they can achieve their goals.
Rick Presley and Don Deptowicz thank all the attendees who stopped by. Renaissance Services will be back in 2025.
Click here to access info about Renaissance Services’ rapid parts casting and reverse engineering solutions.
Click here for a link to Renaissance Services’ blogsite.
For further information about any of Renaissance Services’ products or services, please contact Rick Pressley at (937) 586-7277 or email Renaissance Services at [email protected]